⊙자동차 Body 구조화 기술
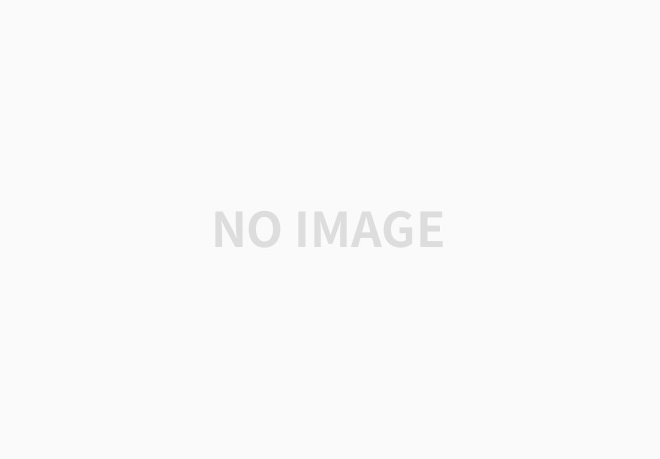
자동차 Body에는 Body On Frame Type과 Monocoque Body Type이 있다.
Body On Frame Type은 뼈대인 프레임을 자동차의 하부에 덧댄 차량의 형식이다. 마차 시대부터 사용되어 온 가장 전통적인 차체 구조로 사다리꼴의 프레임에 파워트레인과 차량의 바디를 올리는 형식이다. 장점은 높은 강성에 있다. 충격의 흡수를 차량의 바디가 아닌 하부 프레임이 담당하기 때문에 노면 충격에 대한 내구성이 우수하다. 또한 모노코크와 반대로 사고가 발생했을 때 차량의 프레임과 바디를 분리해서 수리가 가능하기 때문에 정비성이 우수하다는 장점이 있다. 내구성이 강한 프레임 바디 차량은 그에 따른 단점도 가지고 있다. 철로 이루어진 프레임은 무거운 중량 덕분에 연료 효율과 운동성능이 떨어진다. 효율이 떨어지는 프레임 바디 차량은 갈수록 거세지는 환경 규제 앞에서 점점 설자리를 잃어가고 있고 그나마 남은 몇 안 되는 프레임 바디 차량도 후속 모델을 모노코크 형식으로 바꿔 출시하고 있는 추세다.
Monocoque Body Type은 승용차에 주로 사용되는 일명 '일체형 차체'다. 과거에 항공기에서 처음 접목되던 섀시 기술이었으며 이후 자동차로 넘어와 널리 쓰이기 시작했다. 모노코크의 가장 큰 장점은 가벼운 무게다. 별도의 하부 프레임이 없고 차체가 하나로 이어져 있기 때문에 중량이 가볍고 동시에 차체의 밸런스가 뛰어나다. 모노코크는 자동차가 대중화된 이후로 가장 많이 사용되고 있다. 제조사가 차량을 생산할 때 모노코크 바디는 프레임 바디에 비해 제작 단가와 시간이 절약된다는 것이 장점이다. 모노코크 바디는 도로의 충격을 차체로 잘 분산시키고 동시에 충격을 흡수하는 능력이 뛰어나 승차감이 우수하다. 별도의 프레임이 없기 때문에 침범하는 실내공간도 없어서, 차량의 실내를 넓게 뽑아낼 수도 있다. 승용차와 SUV 등 차량의 형태에 제약이 없이 사용이 가능해 최근 출시되는 대부분의 신차는 모노코크 바디를 형식을 채택하고 있다. 물론 모노코크 바디에도 단점은 있다. 모노코크 바디는 '일체형 차체' 형식을 하고 있기 때문에 프레임 바디에 비해 강성이 약하고 사고 시 차체가 변형될 수 있다. 만약 사고로 인해 모노코크 차량의 차체가 변형될 경우 원상태로의 완벽한 복구가 어렵다.
⊙Safety Zone과 Crushable Zone
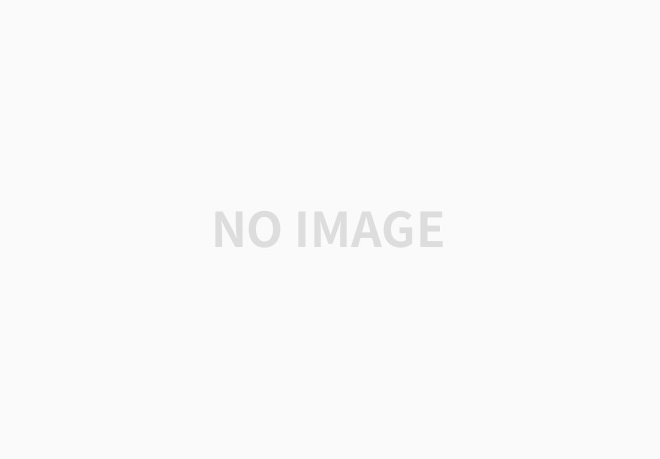
자동차는 잘 부서지는 차량이 좋을까? 아니면 안부서지는 차량이 좋을까? 역설적으로 탑승자의 보호를 위해 잘 부서지는 차량이 좋다. 하지만 탑승자의 보호를 위해 최종적으로는 부서지면 안되는 곳도 있다. 그곳을 Safety Zone이라 부르고 잘 부서지는 부분은 Crushable Zone이라 부른다.
Safety Zone : 탑승자를 보호하기 위해 초강력 강판 또는 보강재로 격자모양을 구성한 부분
Crushable Zone : 엔진룸 부분과 트렁크 부분은 충돌 시 충격을 잘 흡수하도록 설계
⊙Body의 각 부위 명칭
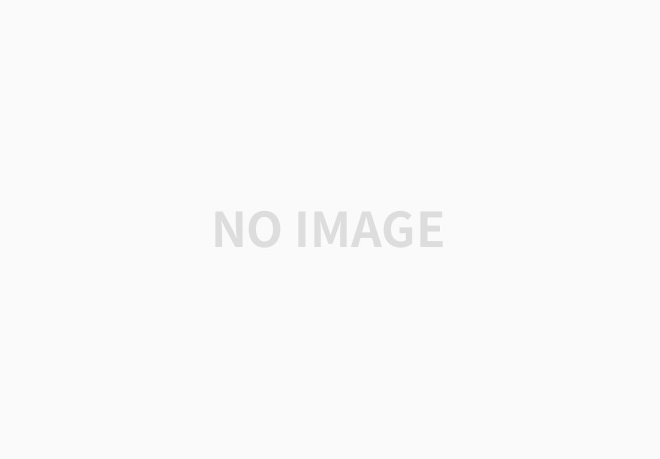
필러는 기둥에 따라 각각 a, b, c 총 3개가 있다. 차의 밑부분 바퀴 위쪽으로 올라오는 부분은 언더바디인데 매우매우 중요한 요소이다. 각 패널 역시 중요하고 특히 중요한 론지판넬은 탑승자의 안전을 위해 사고가 발생할 시 무조건 아래로 휘게 돼있다. 위로 휠 시 운전자에게 매우매우 위험하기 때문이다. 휠 하우스는 바퀴를 둘러싸고 있는 부분을 말한다. 사진에 나오지 않은 다른 것은 다 보강판넬(Reinforce)이다. 트렁크 뒤쪽에 스포일러 판넬이라고 있는데 와류현상을 막기 위해 존재한다.
⊙Body의 제조 기술
각 부품을 조합하는 공정은 용접과 Sealing 공정이 사용된다. 우리나라는 점(Spot) 용접을 쓰고 있는데 이유는 co2용접을 하게 되면 모재가 두꺼워야 한다. 원래 제품으로 쓰려고 하는 강판이 두꺼워야만 co2용접을 할 수 있는데 얇을 경우 구멍이 생기게 되고, 변형이 크게 된다. 그래서 점용접을 하게 되면 사이사이가 비게 되기 때문에 점용접을 하게되면 Sealing을 해줘야 한다. 만약 이걸 피하고 싶으면 레이저로 하면 되는데 그렇게 되면 시간이 상당히 많이 걸린다. 그래서 독일의 경우 루프쪽은 레이저용접을 하고 나머지는 점용접을 하고 있다. 여기서 Sealing이란, Body의 착도장이 완료된 후 녹슬기 쉬운 부분에 실리콘으로 도포하는 공정을 의미한다. 씰링(Sealing)의 첫번째 목적은 방수이다. 두번째는 방청이다. 여기서 청은 녹을 의미한다. 조직과 조직 사이를 파고들어 발청을 유발하는데 이걸 크레바스 발청이라고 부른다.
세번째는 방음이다. 이 세가지의 이유로 용접 후에 사이를 씰링으로 막는 것이다.
⊙표면처리 기술
사용한 금형이나 사용할 소재의 표면을 청소하거나 제품의 부식 , 방충, 방화, 장식의 목적으로 표면에 화학적, 물리적, 처리를 하는 것을 의미한다. 도장, 도금, 화성처리법, 라이닝법 등이 존재한다. 제조업에서 표면처리는 부식의 방지, 표면의미적인 기능의 추가, 내 마모성, 내유성, 내화학성 기능 추가 이다. 내화학성의 대표적인 예는 겨울철 사용하는 염화칼슘 등으로 인해 발생한 것이다.
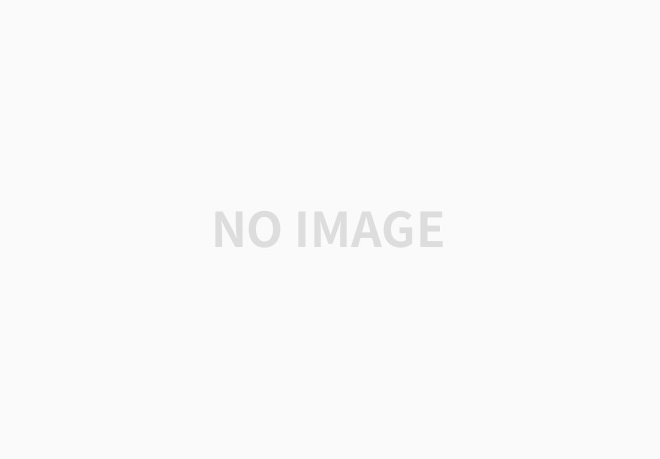
유리처럼 매끈히 표면처리한 소재들도 확대해서 보면 많은 흔적이 있다. 도장은 소재의 표면 위에다 도장의 막인 도막을 씌운다. 도막은 두께와 경도가 상당히 중요한데 두 가지 성질은 상관관계가 있다. 양의 상관관계, 음의 상관관계가 있다. 망치로 때려서 충격이 가해지면, 도막이 깨져 부식이 생긴다. 분체 도장은 분말로 열을 가해 표면에 도장한다. 도장은 크게 상도 중도 하도가 있는데 전착도장은 하도이다. 도막이 결국에는 층인데 전착이 하부에 깔리 프라이머가 중도에 깔리고 유색층인 상도가 있다. 프라이머가 중도인 이유는 상도와 하도 둘 모두와 친하다. 하지만 상도와 하도는 서로 친하지 않다. 도막층이 서로 단단하게 하려고 이러하게 구성됐다. 전착 과정에서 바디를 걸어놓는 행거에 플러스 전하를 걸어두고, 도료에 마이너스 전하를 걸어 서로 잘 반응하게 한다. 여기서 조심해야 할 것은 스프링 등이 전착 과정에서 수소 취성에 의해서 손상될 수 있다. 그래서 절대 스프링력이 가해진 상태에서 전기를 사용하면 안된다. 전기가 통하지 않게 고무 등을 통해 이격시켜야 한다. 원자중 가장 작은 수소는 금속격자 사이를 쉽게 원자상태로 뚫고 들어가기 때문에 플라스틱에도 수소취성이 발생하여 플라스틱도 쉽게 부러진다. 전착과정을 끝낸 바디는. 반드시 건조로를 통과해야 한다. 건조로에는 두가지가 있는데 하나는 분위기로가 있고 두번째는 직화로가 있다. 분위기로는 열을 가할 수 있는 시설을 통해 주변의 온도를 뜨겁게 해 열을 가해지도록 한다. 직화로는 직접 불로 가열하는 방식이다. 도장의 건조로는 분위기로를 사용한다. 그 이유는 도장이 타버리기 때문이다. 가열 구간과 홀딩구간에 있는 시간에 따라 달라진다. 로가 기본적으로 터널식으로 돼있어서 설비에다 통과시키는 방식인데 중간중간에 온도센서를 심어놔서 각각의 온도를 관리한다. 건조 과정을 거치면 씰링공정을 가고, 중도(프라이머)과정을 거쳐 상도로 가서 색을 입힌다. 그리고 최종적으로 검사 및 수정을 통해 완성이 된다.
도장 과정에서 불량이 발생하는데 어떤 유형이 있고 어떻게 예방할 수 있을까?
-오렌지 필 : 오렌지의 표피의 모양과 같은 느낌의 도장면이 형성되는 결함으로 유분의 유입이 그 주된 원인
압축공기에 배기가스 등이 들어가면 오렌지 필이 발생하낟.
-이색 : 색상이 표준과 다른 느낌으로 나타나는 경우로 도료의 배합이 주 원인.
마스터 샘플을 이용해서 다른 색을 잡아낸다.
-오염 : 먼지, 벌레, 뭉친 또는 이전 도장재료, chip 등의 이물질이 유입되어 도장면에 나타나는 결함
-도막두께 불량 : 형성된 도장 두께가 표준에 미달하거나 과도할 경우의 불량으로 도장 조건 setting 문제임
-도장 누락 : 일부 부분적으로 도장 대상물에 중도, 상도의 도장이 누락 될 경우로 작업자 작업 누락이 원인
-도막 꺠짐 : 도막이 너무 두껍게 형성되거나 열적, 물리적 충격, 도장물의 변형 등으로 깨지는 결함
-박리/들뜸 : peel off, 박리 test 를 통과하지 못하는 결함 또는 이미 도막이 도장물에서 분리 되어 있는 불량
-흘러내림 : 도장량이 많아 도막이 흘러내려 물결모양이 나타나는 결함
도금 기술(plating)
어떤 물질의 표면에 금속을 얇게 입히는 것으로 액상, 분말 등 여러 상태에서 도금을 할 수 있다. 호름은 재료입고, 세척, 행거 고정, 도금, 검사 순이다. 도금의 종류에는 전기도금, 화학도금, 융용도금, 증착도금, 분무도금 이 있다.
아쉽게도 전라북도에는 표면처리업체가 많이 없다. 따라서 자동차 업계가 발전함에 따라 표면처리업체가 생겨 경쟁력을 가지게 되었으면 좋겠다.
⊙의장 부품 제조기술
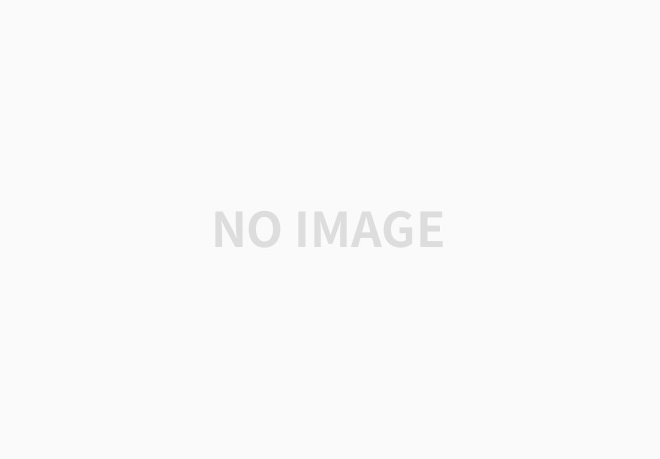
안쪽에 붙는 모든 인테리어는 의장 제품이라고 할수 있다. 의장 제품의 종류로는
-시트
-헤드라이닝
-각종 소음과 진동방지 insulator : 차량의 내측 하단 또는 외측에 부착하여 방음, 방진 기능을 하는 제품이다.
-sun visor
-차량 carpet
-door trim
-Ip : 차 앞쪽에 있는 제품 전체를 통틀어서 말한다. 등이 있다.
인테리어 파트들은 다 의장제품이라 하고, 트림 파트라고 한다. 제일 먼저 트림라인이 깔려야 다음 작업이 진행 되므로 트림라인이 제일 먼저 작업된다. 헤드라이닝은 종이를 압착해서 성형한다. 만약 사고 발생시 플라스틱보다 덜 딱딱한 소재를 사용해서 머리를 보호해준다. 안전성이 좋으면 쿠션이 딱딱한게 좋지만, 대부분들의 운전자들이 선호하지 않으므로 너무 딱딱하게 만들지 않는다.
insulator 제조 기술 및 발포 기술: 흡음재, 단열재, 내 진동 재료 등을 발포재료와 혼합하여 발포금형에 주입 발포하여 제품을 성형한다. 발포 공정에서 발포를 하면서 발포 금형의 내측에 원재료가 잘 붙지 않고 떨어지도록 이형제를 도포해야 한다. 이후 후 공정 필요한 각종 부자재인 wire, 부직포 등을 삽입하여 주입할 수 있다. 이후 일정시간 쩌내면 되는데 금형에서 꺼낸 폼패드는 재료 특성상 공기주머니가 생기는데 이를 터트려 형상을 잡는 크러싱 공정을 거친다. 이후 폼패드는 이물질과 flush를 제거하여 완성된다.
⊙조립 기술(assembly Technique)
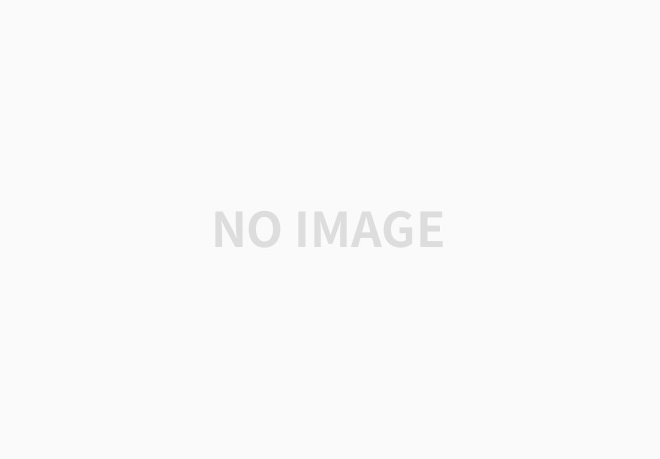
조립 기술 : 자동차 body에 조립되는 부품(Hang on parts)들을 최적 시간내 최저 Manhour로 최적비용으로 효율적으로 체결하는 기술
엔지니어로서 조립공장에서 최우선은 최적화 작업과 표준화 작업이다. 부가가치를 만들지 않는 작업은 낭비이다.
조립 기준 : 기준이 되는 부품, 차량의 경우 body를 mother item으로 하여 달라붙는 부품, hang on part 들을 순서(Sequencing)를 정하여 정해진 방법에 따라 정해진 기구를 사용하여 작업하도록 기준(Standards)을 정한 것.
조립 순서 : 생산해야 하는 완제품의 사양(Option)들을 작업의 조건에 따라 순서를 정하여 생산하도록 작업시시서를 작성 작업현장에 배포한 것을 말하며 완제품을 만들기 위한 조립되어야 하는 부품의 공급순서를 작업지시서와 함께 동시에 작업현장에 배포한 것을 말한다. 생산되는 차종을 옵션에 맞춰 내려주는 것을 작업지시서라 한다.
혼류생산이란 하나의 생산 라인에서 두 가지 이상의 완제품을 동시에 생산하도록 만든 것, 다른 말로는 옵션화생산 또는 시퀀스 생산이라고도 한다.
⊙작업표준이란 작업자가 정확한 작업을 할 수 있도록 미리 정하여 교육 및 연습(OJT)된 작업공정마다 배치되어야 하는 표준 방식을 의미하며, 종류로는 다음의 것들이 있다.
표준작업서 - standardized operation sheet 운영표준 관리자
작업표준서 - work standard sheet
작업지침서 - job instructions sheet 반드시 지침서 형태는 무엇을 what to어떻게 how to 왜 why to 순서로 해야 된다.
검사표준서 - 검사절차서, 검사기준서, 검사성적서, 품질 중점관리, 통계적 공정관리
체크 씨트 (check sheet 작업 이전, 작업 중간, 작업종료 후)
3점5s 점검 표준 류(작업자 담당구역, 장비, 점검 points)
계층적 공정감사 (Layerd Audit Sheet) 여기서 audit 현장작업자는 표준대로 작업, 기록, 구분, 적립
선입선출 표준 (FIFO : first in firts out)
작업자 안전수칙 (Safety Standard)
4m man, machine, method, material 사람 장비 방법 자재를 관리하는 부서들이 존재한다. 사람은 인사팀 장비는 생산기술팀 자재는 생산관리, 구매팀 방법은 스탠다드 표준이다.
표준은 매뉴얼에서 시작해서 프로세스로 갔다 프로시듀어 마지막으로 스탠다드 즉 표준으로 간다. 각각의 과정은 시스템표준 절차표준 기준표준 방법표준이다. 책임이란, respose + ability = reponsibilty 책임이 주어졌다는 뜻은 어떠한 능력을 절차에 따라 부여받은 걸 의미한다. 따라서 책임은 응답성이다. 응답성을 따질 때는 신속성, 정확성, 효율성 전체가 요구되고, 최종적으론 품질이 된다. 즉 4m의 기준을 정한다는 것은 작업자 측면에서는 작업표준이고, 방법적인 측면에서는 표준작업이고, 장비적인 측면에서는 보전표준, 일상점검표준, 셋업표준 즉 지침서 표준이고, 자재 표준은 생산관리 표준이다.
이송장비란 Mother item을 기준으로 이송하는 컨베이어, agv, 지게차, 트랙터, 대차, 호이스트 등을 지칭한다. 앞으로 전기자동차는 agv 방식으로 할 가능성이 크다. 전기자동차를 agv에 싣고 하나하나 조립할 가능성이 크다. 그래서 한 팀이 차 한대를 조립하는 식으로 할것이다.
조립 보조 장비에는 보조 이송장비와 보조기구가 있다.
보조 이송장비 : 작업자가 들기 어려운 자재나 중량물을 작업자를 보조하여 이송 시키는 장비를 말한다.
보조기구 : 자재를 고정해주는 fixture와 조립각도나 형태를 잡아주는 역할을 하는 Jig, 조립성을 도와 보조해 주는 Guide, 열림 또는 닫힘 등을 유지시켜 주는 support, 작업잦의 육체적 피로를 줄여주는 보조장비 등이 있다.
표준작업서와 작업표준서에 대한 내용은 매우 중요하기 때문에 따로 포스팅 할 계획이다.